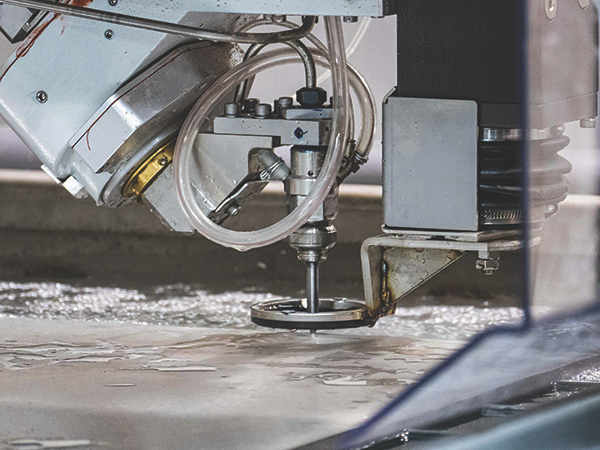
How likely is a UK engineered stone ban?
With engineered stone surface bans abroad making headlines, could similar legislation come to the UK? Andy Phillips, director and co-founder of the Worktop Fabricators Federation (WFF) offers some advice to concerned retailers
Solid, stable, profitable and visually exciting quartz worktops suddenly became front-page news at the end of 2023 for all the wrong reasons. Major Australian retailers and then the Australian government announced a country-wide cancer-scare product ban. This immediately raised questions with UK showrooms and interior designers.
First things first: ‘cancer risk’ headlines always make for compelling reading. But, it needs to be emphasised that any risks from crystalline silica dust occur only when the surface is cut by fast moving abrasive tools in the factories where the worktops are cut, shaped and polished prior to installation.
This process flings small fragments of crystalline silica into the air where it can be breathed into the lungs. It is this respirable crystalline silica that can then create a health risk.
Risk management
There is no risk to consumers, specifiers or installers in using these products. No question of having to rip out existing work surfaces or interior features. There are no great risks associated with conventional demolition or removal, provided the worktops are not cut with machine grinding tools.
So, what are the chances of the UK Government following suit with Australia? Very slim, as far as we can see. The Health & Safety Executive has always been highly aware of the risks from respirable dust, and silica dust in particular. Current Health and Safety Executive guidance for factory owners and enforcement teams reads that: “Products containing silica can be processed safely when proper controls are put in place.”
If you’re running a stone-cutting workshop, ‘proper controls’ are a recognised cost of doing business – they’re what keep you and your workforce safe. If, on the other hand, you are making stone worktops out of the back of a van with modified joinery tools or an angle grinder, ‘proper controls’ are something of an optional – and costly – extra.
Without proper controls, such workers will almost certainly exceed the daily exposure limit set out by the Health and Safety Executive as soon as they start work. Most professional fabricators, by contrast, are wet-cutting their worktops in controlled factory conditions, accompanied by rigorous health and safety monitoring. This suppresses dust at point of source, and prevents it from getting into the atmosphere in the first place.
Political intervention
You can never say ‘never’ in politics, of course. Especially with an election looming. But if there were any escalation of interest among UK legislators, their most obvious first step would be to revisit last January’s All Party Parliamentary Group’s report on Improving Silicosis Outcomes in the UK.
Again, the core recommendations are all to do with preventative measures on the production line: better staff education, more monitoring, regular health checks and reduced occupational exposure.
From the industry’s point of view, the most immediate, most proportionate and most useful regulatory intervention would be to restrict the sale of worktop blanks to fabricators who can demonstrate they are operating suitable H&S policies in suitably equipped premises. In other words, outlaw the ‘make-at-home’ option. In addition to this, the fabrication industry supports a move to lower silica products where these are available.
But why does the make-at-home option exist at all? Because customers want top-quality aesthetics at rock-bottom prices. If you can’t shave the cost of the raw materials, you have to shave the cost of processing and the accompanying ‘suitable controls’. If the retail showroom is the principal contractor, they carry a statutory duty to ensure their subcontractors are following correct HSE regulations.
Concerned retailers and specifiers should exercise their duty of care by ensuring they buy only from fabricators who can demonstrate a commitment to health and safety – including proper factory controls for dust, and ensuring any on site cutting is minimised and the risks of RCS managed.
Quartz queries
There are also plenty of options instead of quartz, from naturally quarried granites, marbles and quartzites to modern engineered porcelain and sintered stone worktops, which technically have more in common with ceramic floor tiles than with natural stone. The latter, in particular, is increasingly the choice for professional commercial kitchens.
Most of these materials contain significantly less crystalline silica. In addition to this, some ‘quartz’ is being reformulated to reduce the silica to very low levels by replacing the minerals with other materials.
But there’s a reason quartz worktops dominate the UK market. The main one is design consistency: they deliver a genuine ‘stone’ aesthetic, with all the advantages and consistencies of factory-engineered products. Development by the leading quartz companies has expanded the solid stone market.
Colour, texture, porosity, patterning and dimensional stability are not products of random nature, but of precise engineering, as well as extensive research and development. Quartz is a product with which showrooms are familiar, consumers are comfortable and fabricators’
machine minders are confident in processing.
Natural stone and sintered stone products have advantages and peculiarities of their own. And in the same way, it might be wise for showrooms to invest a little more into understanding the provenance of their quartz products. Maybe this is a good time to revisit the alternatives, too? Either back to the comfortable, ‘sustainable’ values of natural stones, or forward to the increasingly sophisticated and competitive engineered clay alternatives.